Ahascragh Distillery is first to produce carbon-neutral spirits in Ireland
With support from SEAI, the award-winning eco-distillery is powering their new production facility and visitor centre using renewable energy.
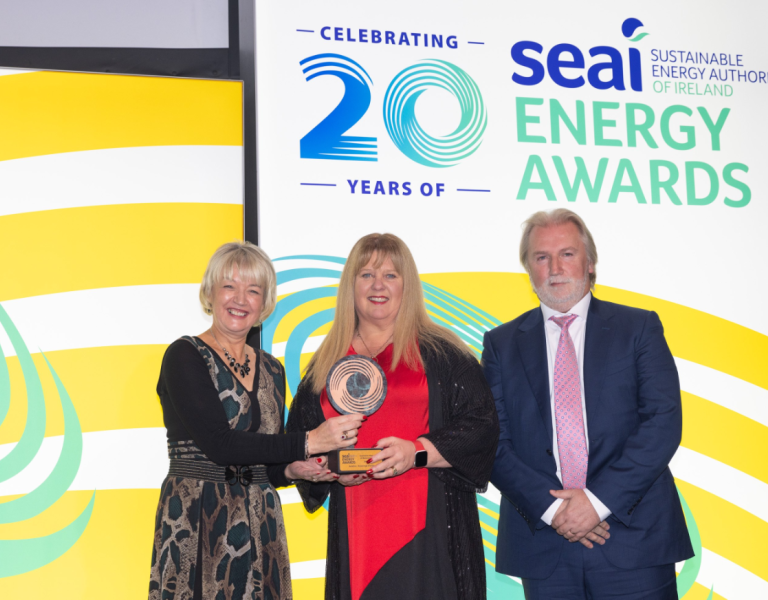
Background
A husband-and-wife team, Gareth and Michelle McAllister, have lived and worked in countries across the world. They are now turning their passion for Irish spirits into a family-run distillery business in Ahascragh, Co Galway.
In 2020, they took on the construction and redevelopment of an old mill, which dates to the early 1800s. They gave it a new lease of life as a visitor destination and the distillery and visitor centre officially opened its doors in July 2023.
The project
The McAllisters' goal was to distil the first zero-emissions spirits in Ireland and change from an energy intensive process to producing Irish whiskey in a more sustainable and environmentally friendly way.
A huge part of achieving that goal was down to their distillery building itself. Instead of constructing a new building, they renovated an old mill using energy efficiency design (EED) principles. They worked with SEAI's Excellence in Energy Efficiency Design (EXEED) programme team to achieve this.
SEAI provide grant support for projects, which are following the EXEED Certified standard. This includes major renovation and major energy upgrades of existing buildings and assets.
In 2022, SEAI provided the Ahascragh Distillery project with grant support of €500,000 through the EXEED Grant programme.
Renewable energy
Both Gareth and Michelle wanted to power the distillery using renewable energy and this became possible using new technology that combines high temperature heat pumps with an innovative energy storage system.
Heat is provided to the distillery through heat pumps which means that there will be no flue related emissions or impacts on the local environment.
The heat pump design, heat recovery and thermal storage means that the energy inputs to the distillery are a third of what would be used by traditional technology.
Results
Ahascragh Distillery's work to date has delivered excellent results:
- The peak heating and cooling demand has more than halved.
- Unlike other distilleries in Ireland, the heat delivered to the distillery does not require the combustion of any fossil fuels and uses green electricity.
- The heat source for the heat pump technology is the waste heat from the distillation process resulting in an innovative continuous closed efficient heat recycling method.
- The building itself has been protected with much of the original machinery and with wooden beams being restored and reused.
These activities combined deliver lower energy bills and lower carbon emissions.
This distillery is an innovative example of what all Irish industry should be considering to cut costs and carbon at the same time. Electrification of heat should be the cornerstone of reducing costs and carbon emissions. I feel in Ireland, industry needs to catch up and very high temperature heat pumps like those deployed at Ahascragh, coupled with a very efficient energy storage system, is an example of exactly what Irish industry needs.
EXEED process
The EXEED process ensured that energy efficiency and renewable opportunities were identified and maximised at the earliest stage of the project.
Ahascragh Distillery is an excellent demonstration of a project that has gone through the EXEED process. It's design has yielded a solution that recycles energy that would normally be rejected, making the process significantly more efficient than a conventional design would have been.
The distillery is compatible with a broad range of renewables and there is massive scope for replication of this approach throughout the food and drink industry.