Roadstone Ltd. optimises its asphalt process
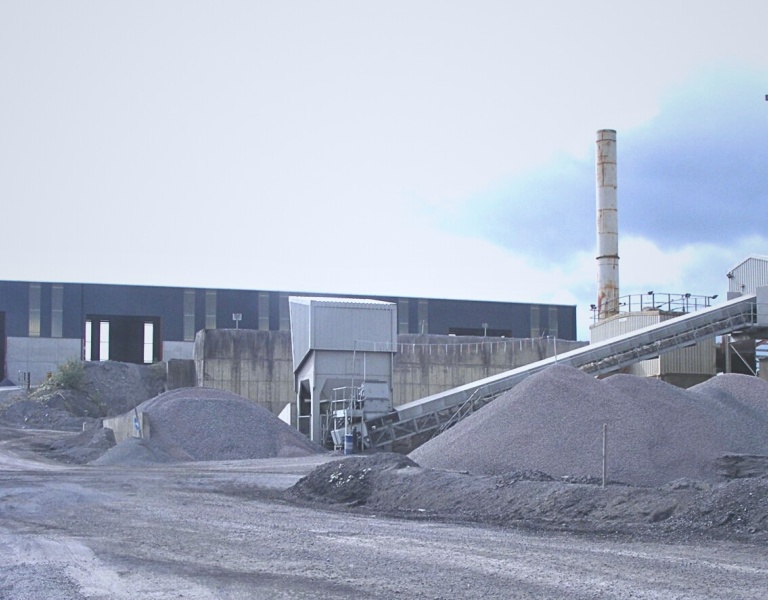
Roadstone Ltd. is a leading producer and supplier of building and construction materials in Ireland.
As part of the CRH Group, Roadstone implemented group-wide energy and resource efficiency programmes to help achieve a more energy-efficient, resilient, and sustainable built environment.
Background
Since 2007, Roadstone has implemented structured energy management across its operations. 22 Roadstone locations throughout the country, including The National Transport Division, are accredited to ISO 50001 - the internationally recognised Energy Management Systems standard.
SEAI's Excellence in Energy Efficiency Design (EXEED) Certification is the next milestone in the development of Roadstones' maturing Energy Management System with the aim that all future significant energy management projects will achieve EXEED Certification.
It is anticipated that this project will become the template for other energy projects across the business. Roadstone uses the EXEED approach to highlight and implement energy efficiency measures that may not be identified under normal business practices.
The project
In 2016, SEAI introduced the EXEED process to Roadstone. As part of the EXEED approach, several opportunities were identified as having the potential to save energy within the business production process.
These opportunities were recorded in the Energy Savings Register (ESR) - a key document in the EXEED process. Improvement projects were discussed further and the most appropriate were included in a Project Execution Plan (PEP) delivered by the in-house EXEED Project Team.
The analysis of Roadstone's business activities quickly identified the asphalt process as a significant energy user (SEU). An energy balance report for Roadstone's production activities showed that in 2018 asphalt production accounted for around 40% of Roadstone's total annual energy use i.e., approximately 160 GWh. Therefore, asphalt production would become the focus of the initial EXEED project.
Asphalt production
Asphalt is used in building transport infrastructure, including roads, car parks and runways. The asphalt production process is carried out across multiple Roadstone locations.
The EXEED approach for optimising the production of each asphalt producing site is broken into two stages. The first stage was identified in the Energy Saving Register. It involves implementing control measures that regulate input temperatures; this includes dryer modifications. Asphalt needs to be dried at a high temperature to remove all moisture in the raw material.
Dryer modifications and upgraded controls allow Roadstone to reduce fuel consumption by creating a more controlled environment. It also increases the possibility of adding recycled asphalt paving material that would normally be sent to landfill.
The second stage (or opportunity), involves using data and intelligent software that will build algorithms that communicate issues that are affecting performance within the production process. The Energy Saving Register found that accurate energy and plant performance data makes it easier to demonstrate and quantify the viability of the application of renewable energy solutions.
For Roadstone Limited, EXEED has become more a way of routinely managing the entire production aspects of the company, not just energy management aspects.
Results
To date, Roadstone have achieved annual savings of 24 GWh across 11 sites where the measures have been implemented. The estimated annual energy savings on completion of the implementation of the EXEED process at 11 Asphalt Production sites is 50 GWh.
By recycling the asphalt, Roadstone improve material circularity which also results in decarbonisation of products going to the market..
The application of the EXEED framework resulted in additional benefits for the company. It supported the management of the production process and helped boost the sustainability of the overall business service.
What's next?
The goal is for all 11 Roadstone sites to achieve EXEED certification. There are currently 7 sites undergoing certification audits, expected to be completed by end of June 2024. The remaining sites expect to be certified by June 2025.
This is an ongoing, value-added stream project that is being developed as a multi-year investment programme at all 11 asphalt producing locations throughout Ireland between 2016 and 2030.
Furthermore, there is a 10-year strategy to implement the EXEED process for all products across all locations throughout Ireland. This will include other opportunities identified in the Energy Savings Register by the EXEED project.
Read about the EXEED programme